DESCRIPTION
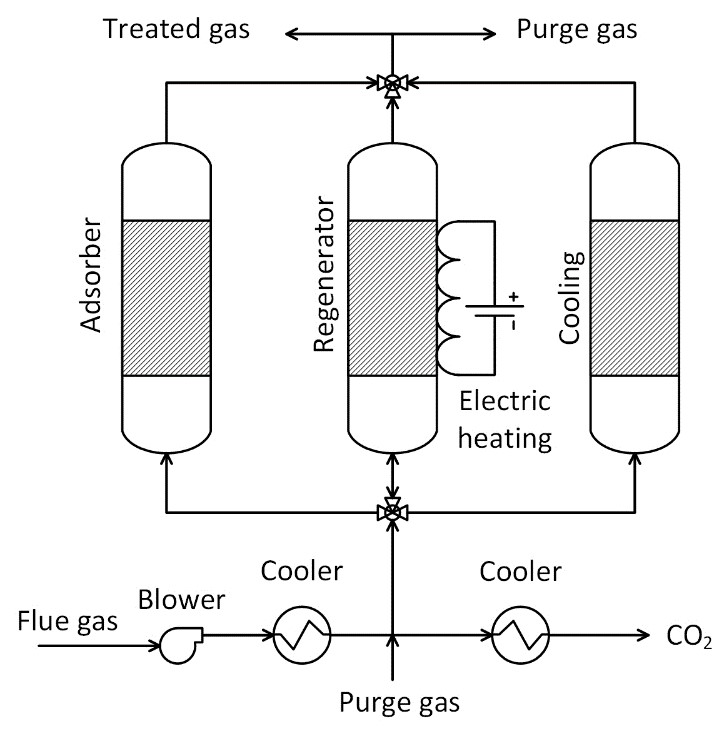
TECHNICAL ASPECTS (all % are volume-based)
Point sources: Power plants1, oil-fired power plant2, Pulp & paper, biomass, oil & gas, steam-methane reforming, lime, steel, cement, petrochemicals3. (same as TSA)
CO2 concentration range: 1%-10%2
CO2 capture efficiency: ~80%4
CO2 purity: 80%4
Min. feed gas pressure: 1.1 bar2 (to overcome pressure drop)
Max. feed gas temperature: 40 °C4
Typical scale: Potentially large (1.6 MtCO2/yr) *
Primary energy source: Electricity2
Impurity tolerance: Adsorbent dependent.
*CAPTIN project – Joule ESA
FUNCTION IN CCU VALUE CHAIN
- Capture CO2 from flue gases.
- Adsorbents such as zeolites are highly affected by the presence of water in feed gas, requiring an upstream dehydration step.
- Poisoning of adsorbents due to impurities such as SOx and NOx requiring appropriate pre-treatment steps.
LIMITATIONS
- Cycle times of minutes are necessary for the large-scale deployment of ESA systems in CO2 capture.
- Adsorbent material may degrade over time, reducing overall capture efficiency.
- Higher capital cost and spatial footprint due to longer cycle times and larger beds.
ENERGY
- Electricity is used by the blower to raise the flue gas pressure to overcome the pressure drop in the reactor bed.
- Steam may be required for regeneration if an adsorption-based dehydration unit is used upstream of the capture unit.
- Electricity is used during regeneration by ohmic heating.
CONSUMABLES
- Adsorbent with a certain replacement period.
- Cooling water may be required to cool the feed gas in a direct contact cooler and after the blower.
Parameter | Value |
---|---|
Electricity (kWh/tCO2) | 567 a, 4 |
Aux. electricity (kWh/tCO2) | 60 b, * |
Cooling water (t/tCO2) | 47 c, * |
Adsorbent (kg/tCO2) a | 0.4 d, * |
Steam (t/tCO2) | 0.45 e, * |
a Regeneration electricity using Zeolite 13X and activated carbon 70:30 wt.%. b Electricity for pumping and blower c Cooling water for flue gas and CO2 cooling. d Replacement period of 5 years. e Steam for regeneration upstream flue gas dehydration unit. *CAPTIN project – Joule ESA |
COSTS
CAPEX: ~7.5 €/tCO2*
Main CAPEX: Adsorption reactors with initial adsorbent inventory and blower.
CAPEX may be underestimated because it accounts only for material costs and assumes the use of carbon steel for the reactors.
OPEX: ~93 €/tCO2*
Main OPEX: Electricity, steam, and cooling water.
CO2 capture cost: ~100.5 €/tCO2*
Depends on regeneration energy, CO2 concentration, and electricity price.
*CAPTIN project – Joule ESA; CO2 concentration – ~4.6 vol.%; capture capacity – 1.6 MtCO2/yr; capture efficiency – 90%; adsorption time – 960 s; desorption time – 960 s; cooling time – 1200 s; ohmic heating efficiency – 90%; 2020 euros; discount rate – 7.8%; WACC – 4.1%; plant lifetime – 30; years; installation factor – 4; electricity price – 100 €/MWh; steam – 25 €/t; cooling water – 0.32 €/m3; adsorbent – zeolite 13X; adsorbent price – 4600 €/t.
CO2 avoidance cost: 127.5 €/tCO2 avoided 5 **
** Estimated for only the ESA case with the NGCC power plant
ENVIRONMENTAL
CO2 footprint: 126.5 kgCO2eq/tCO2 captured *
Estimate includes electricity (53% at 0.107 tCO2eq/MWh) and steam (47% at 0.135 tCO2eq/ton). LCA data not available.
Spatial footprint: 456 m2 for 1.6 MtCO2/yr *
*CAPTIN project – Joule ESA results: cyclic operation; number of reactors = 52; only reactor footprint; reactor diameter = 3.35 m; height = 10 m.
Environmental issues: Disposal or recycling of spent adsorbents.6
ENGINEERING
Maturity: Under development (TRL 4-5)5,7
Laboratory experiments have been performed.
Retrofittability: Potentially feasible
Electricity is the main energy source; phased implementation due to its modular nature; handles flue gas impurities.
Challenges due to large spatial footprint requirement.
Scalability: Potentially High
Well suited for capturing CO2 at a wide capture rate range due to its modular nature.
Process type: Solid stationary adsorbent-based without chemical reactions.
Deployment model: Centralized only.
Each column with adsorbent undergoes cyclical CO2 adsorption and desorption.
Technology flexibility: Hybridization with other capture technologies is feasible. It can be used to increase CO2 concentration.
TECHNOLOGY PROVIDERS
- Electrified CO2 concentrator by SUSTEON, US
ALTERNATE PROCESSES
Induction and microwave heating swing adsorption (IHSA and MWSA)
IHSA and MWSA segregate CO2 from flue gas at near ambient pressure. The CO2 is desorbed by applying an electric field via inductive heating or microwave radiation. The adsorbent used for IHSA is a ferromagnetic zeolite 13X, while the one used for MWSA is activated carbon. The data shown below belongs to IHSA, while the value in parentheses belongs to MWSA from the CAPTIN project.
CO2 concentration: 4.6 vol.% (4.6 vol.%) *
CO2 purity: 100% (100%) *
CO2 capture efficiency: 90% (90%) *
Desorption time: 720 (480) seconds *
Heating efficiency: 90% (60%) *
Electricity: 1000 (1000) kWh/tCO2 captured *
Aux. electricity: 60 (60) kWh/tCO2 captured *
Cooling water: 47 (47) t/tCO2 captured *
Adsorbent: 0.4 (0.7) kg/tCO2 captured *
Steam: 0.45 (0.45) t/tCO2 captured *
CAPEX: ~7 (~14) €/tCO2 *
OPEX: ~121 (~121) €/tCO2 *
*Electricity is ~88% (~88%) of OPEX with electricity price of 100 €/MWh; installation factor – 4; adsorbent - ferromagnetic zeolite 13X (activated carbon); adsorbent price – 5000 (1000) €/t.
CO2 footprint: 173 (173) kgCO2eq/tCO2 captured *
Spatial footprint: 421 (825) m2 for 1.6 MtCO2/yr *
Maturity: Under development (TRL 4-5)
Technology providers: No technology providers yet.
*CAPTIN project – IHSA (MWSA) results: CO2 footprint estimate includes only electricity (0.107 tCO2eq/MWh) and steam (0.135 tCO2eq/t). LCA data not available. Cyclic operation; number of reactors = 48 (44); only reactor footprint; reactor diameter = 3.35 m; height = 10 m.
CONTACT INFO
Mohammed Khan (mohammednazeer.khan@vito.be)
Miet Van Dael (miet.vandael@vito.be)
ACKNOWLEDGEMENT
This infosheet was prepared as part of the MAP-IT CCU project funded by VLAIO (grant no. HBC.2023.0544).
REFERENCES
1. Grande CA, Rodrigues AE. Electric Swing Adsorption for CO2 removal from flue gases. Int J Greenh Gas Control. 2008;2(2):194-202.
2. Zhao R, Liu L, Zhao L, Deng S, Li H. Thermodynamic analysis on carbon dioxide capture by Electric Swing Adsorption (ESA) technology. J CO2 Util. 2018;26(May):388-396.
3. Barlow H, Shahi SSM. State of the Art: CCS Technologies 2024.; 2024.
4. Grande CA, Ribeiro RPPL, Rodrigues AE. CO2 capture from NGCC power stations using Electric Swing Adsorption (ESA). Energy and Fuels. 2009;23(5):2797-2803.
5. van der Spek M, Ramirez A, Faaij A. Challenges and uncertainties of ex ante techno-economic analysis of low TRL CO2 capture technology: Lessons from a case study of an NGCC with exhaust gas recycle and electric swing adsorption. Appl Energy. 2017;208:920-934.
6. De Coninck H, Benson SM. Carbon dioxide capture and storage: Issues and prospects. Annu Rev Environ Resour. 2014;39:243-270.
7. Voskian S, Hatton TA. Faradaic electro-swing reactive adsorption for CO2 capture. Energy Environ Sci. 2019;12(12):3530-3547.