DESCRIPTION
This infosheet contains information on chemical absorption technology employing all the amines other than the MEA solvent (see dedicated infosheet on MEA-based technologies). The other amines include secondary and tertiary amines, their blends, and mixtures including different additives. More information on various amines is given in this review paper.1 The information provided here is for the amine-based solvents, which are publicly available or from the main technology providers. The process is similar to that of MEA-based technology as shown in the Figure below. The flue gas is sent to the absorber column, where it flows upward and comes into contact with the down-flowing aqueous amine solution. The CO2 in the feed gas reacts with the amine to form a CO2-rich solution. This solution is then heated in a regeneration column to release a pure CO2 stream and regenerate the amine for reuse. For amine-based technology, there are various influencing factors towards specific energy consumption, namely CO2 partial pressure with respect to the type of applications, type of amine used, specific heat integration concept, etc.
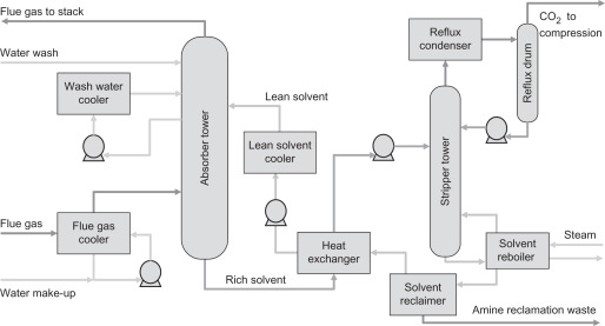
TECHNICAL ASPECTS (all % are volume-based)
Point sources: Power generation, cement/lime production, petrochemical & refineries, iron and steel, hydrogen generation, waste to power facilities.2
CO2 concentration range: 2-30%2 (typical), 0.1-70% (OASE)2
CO2 capture efficiency: >99%2
CO2 purity: >95%3
Min. feed gas pressure: 1.0 bar4
Max. feed gas temperature: 60 °C5
Typical scale:
Large (1 MtCO2/yr for ADIP Ultra by Shell)2
Medium to large (75 ktCO2/yr – 6 MtCO2/yr for CANSOLV by Shell)2
Small to large (3 ktCO2/yr – 3 MtCO2/yr for OASE® Blue by BASF)2
*Calculated based on 300 operational days per year.
Primary energy source: Thermal (steam)
Impurity tolerance: NOx = 20 ppm, SOx = 10 ppm, O2 = minimum possible or use of O2 inhibitors.6 (assumed same as for MEA)
Cansolv: SO2 - 15-60 ppmv7; PM - <20 mg/Nm3; prescrubber removes 90% of SO2 and NO28; Remaining SO2 in feed gas is converted to sulfite in CO2 absorber.7
FUNCTION IN CCU VALUE CHAIN
- Capture CO2 from flue gases.
- Some solvents may be highly affected by flue gas impurities, requiring several pre-treatment steps depending on the impurity.
- Cansolv also removes other gases, such as SO2, if present in small quantities.7
LIMITATIONS
- Tertiary amines have slower reaction kinetics compared to primary and secondary amine processes, often requiring larger absorption columns.
- Although tertiary amines require less energy for regeneration than primary or secondary amines due to their lower heat of absorption, the overall energy consumption is still significant.
- Aqueous amines can corrode equipment, especially with flue gas impurities like SOx, NOx, and O2.
ENERGY
- Thermal (steam) is used for the regeneration of the solvent.
- Electricity is used for operating pumps, blowers, and control systems.
CONSUMABLES
- The solvent is used as a medium to capture CO2. Some solvents may be lost and need make-up.
- Water is used in the process as a solvent diluent for the amine solution.
Parameter | Value |
---|---|
Heat (GJ/tCO2) |
OASE® Blue – 2.59-2.710 ACC™ S21 & S2611 – 3.4 MDEA (10%) + PZ (30%)12 – 1.9 Cansolv DC-1038 – 2.92 Cansolv DC-2018 – 2.33 Piperazine – 2.99 – 3.04 – 2.72 – 2.8513 MHI KS-1™ - 2.153,14 |
Electricity (kWh/tCO2) |
OASE® Blue – 13510 MDEA (10%) + PZ (30%)12 – 224 Cansolv15 – 107.6 (69% compression) Piperazine – 107 – 81 – 74 – 7113 MHI KS-1™ – 1863,14 |
Solvent makeup (kg/tCO2) |
Cansolv DC-1037 – <10%/yr ACC™ S2111 – 0.5-0.6 ACC™ S2611 – 0.2-0.3 MDEA (10%) + PZ (30%)12 – 0.92 |
Cooling water (t/tCO2) |
OASE® Blue – 1.6310 (makeup) Cansolv DC-1038 – 44.4 Cansolv DC-2018 – 32.3 MHI KS-1™ - 2.63,14 (makeup) MDEA (10%) + PZ (30%)12 – 5.3 (makeup) |
10 OASE blue technology; CO2 conc. 21.3%; CO2 purity >99.9%; capture capacity – 1.4 MtCO2/yr; capture efficiency - 95%; electricity includes CO2 compression to 158.5 bar. 11 Aker solutions ACC™ advanced solvents S21 and S26 solvents; CO2 conc. 3.4% and 4%, respectively; without heat integration; 87% capture. 12 CO2 conc. – 20.4%; CO2 capacity – 2227.5 tCO2/day; electricity includes compression to 110 bar. 8 Shell Cansolv; CO2 capacity – 132 tCO2/hr; uses mechanical vapor recompression 13 Piperazine solvent; increasing CO2 concentration 4% - 12% - 20% - 33%; electricity includes CO2 liquefaction at 20 bar and -20 °C. 3,14 Coal power plant; CO2 conc. – 12.3%; 90% capture efficiency; MHI KM-CR Process® with KS-1™ solvent; Heat is calculated from steam consumption (5.9 bar and 160 °C); electricity includes compression power, about 33.3%. |
COSTS
CAPEX:
OASE® Blue: 21.5 €/tCO210
Cansolv: 32.5 €/tCO216
MDEA (10%) + PZ (30%): 10.1 €/tCO212
Piperazine: 13.5 – 7.6 – 6.6 – 5.6 €/tCO213
MHI KS-1: 25.2 €/tCO23,14
Main CAPEX: absorption column, stripping column, and main heat exchanger.
OPEX:
OASE® Blue: 33.4 €/tCO210
Cansolv: 17.4 €/tCO216
MDEA (10%) + PZ (30%): 38.7 €/tCO212
Piperazine: 16 – 13.7 – 11.8 – 12 €/tCO213
MHI KS-1: 17.9 €/tCO23,14
Main OPEX: steam, electricity, cooling water, and amine make-up.
CO2 capture cost:
OASE® Blue: ~55 €/tCO210
Cansolv: ~50 €/tCO216
MDEA (10%) + PZ (30%): 48.7 €/tCO212
Piperazine: 29.5 – 21.3 – 18.4 – 17.6 €/tCO213
MHI KS-1: 43 €/tCO23,14
CO2 avoidance cost:
Cansolv16: 64.4 €/tCO2
Piperazine13: 85 – 69 – 63 – 60 €/tCO2 (estimated)
10 OASE blue technology; Steam-methane reforming plant; CO2 conc. 21.3%; CO2 purity >99.9%; capture capacity – 1.4 MtCO2/yr; capture efficiency - 95%; electricity includes CO2 compression to 158.5 bar; electricity price – 65 €/MWh; lifetime – 30 yrs.
16 Cansolv solvent; Coal power plant; CO2 conc. – 13.3%; 90% capture efficiency; lifetime – 30 yrs; 3.58 MtCO2/yr; 2015 euros; discount rate – 12%; operating hours – 7446 hr/yr; includes compression up to 110 bar; excludes transportation costs.
12 MDEA (10%) + PZ (30%) solvent mixture; CO2 conc. – 20.4%; CO2 capacity – 2227.5 tCO2/d; capture efficiency – 90%; CO2 purity – 98%; includes CO2 compression to 110 bar; electricity price – 58.1 €/MWh; steam price – 22.5 €/t; 90% capture efficiency; 2019 euros; plant lifetime – 25 yrs; interest rate – 15%; CRF – 0.154.
13 Piperazine solvent; values for CO2 conc. – 4%, 12%, 20%, and 33%; CO2 capacity – 0.168, 0.446, 0.709, 1.12 tCO2/yr; piperazine concentration – ~8 mol-PZ/kgH2O; excluding CO2 liquefaction (20 bar and -20°C); including flue gas pretreatment; operating hours – 8000 hr/yr; electricity price – 64 €/MWh; steam price – 5.5 €/t; 90% capture efficiency; 2020 euros; plant lifetime – 20 yrs; interest rate – 6%.
14 MHI KM-CR Process® with KS-1™ solvent; coal power plant; CO2 conc. – 12.3%; 90% capture efficiency; CO2 purity – >95%; 2.99 MtCO2/yr; 2017 euros; CRF – 0.1243; operating hours – 6745 hr/yr; includes compression up to 152.7 bar and 35 °C; process steam at 5.9 bar and 160 °C; excludes transportation costs.
ENVIRONMENTAL
CO2 footprint: Not available. Can be considered same as the MEA-based chemical absorption technology (see infosheet).
Spatial footprint:
Amine scrubbing: 37,500 m2 (250x150) for 2.56 MtCO2/yr, which also includes compression system17 (assuming it to be the same as MEA-based process).
Cansolv DC-103 solvent: 465 m2 for 100 tCO2/day 7
MHI KS-1™ solvent: 19,166 m2 (550x370) for 2.99 MtCO2/yr (including capture island, compression system, cooling tower, and wastewater treatment)14
Environmental issues: solvent emissions, heat stable salts waste, water usage, and wastewater management.
ENGINEERING
Maturity: Commercial (TRL 9)2
Large-scale commercial plants are operational for various solvents.
Retrofittability: Moderate
It can be integrated into existing industrial facilities without substantial modifications to the main process. The heat and electricity sources, and waste removal are required.
Scalability: High
Suitable for both medium and large-scale CO2 capture operations (modular system).2
Process type: Liquid solvent based with chemical reactions.
Deployment model: Centralized or Decentralized.
Decentralized CO2 absorption at point sources with centralized desorption.
Technology flexibility: Hybridization with other capture technologies is feasible. Other technologies can be used to increase CO2 concentration.
TECHNOLOGY PROVIDERS
- CANSOLV by Shell, United Kingdom
- ADIP Ultra by Shell, United Kingdom (MDEA as the main reactant and piperazine as the accelerator)
- OASE® Blue by BASF, Germany
- ASCC by Honeywell, United States
- SUSTENOL™ by Susteon, United States (mixed-amine solvent, regeneration energy = 2.01 GJ/t CO2, capture efficiency = 96.2%, capture cost = €45/t CO2)
- ION solvent by ION Clean Energy, United States (99% capture efficiency; greater stability; low emissions; faster kinetics; low energy requirements)
- CycloneCC™ by Carbon Clean, United Kingdom (uses rotating packed beds and amine-based proprietary APBS-CDRMax solvent; lowers energy demand by 10-25%, reduces corrosion by a factor of 20, decreases degradation by a factor of 10, and has a lifespan that is five times longer than conventional solvents)
- KM CDR Process® by Mitsubishi, Japan
- Just CatchTM and Big CatchTM by SLB Capturi, Norway (formerly Aker Carbon Capture)
- Lummus CO2 recovery by Lummus Technology, United States (up to 97% CO2 recovery)
INNOVATIONS
- Piperazine-activated amine blends: Blending tertiary amines like methyl diethanolamine (MDEA) with piperazine (PZ) has been found to enhance CO2 absorption rates and thermal stability.18
- Amine-based solvents and additives: Enhancing CO2 capture efficiency, reducing energy requirements, minimizing solvent degradation, and mitigating equipment corrosion.19
CONTACT INFO
Mohammed Khan (mohammednazeer.khan@vito.be)
Miet Van Dael (miet.vandael@vito.be)
ACKNOWLEDGEMENT
This infosheet was prepared as part of the MAP-IT CCU project funded by VLAIO (grant no. HBC.2023.0544).
REFERENCES
1. Bernhardsen IM, Knuutila HK. A review of potential amine solvents for CO2 absorption process: Absorption capacity, cyclic capacity and pKa. Int J Greenh Gas Control. 2017;61:27-48.
2. Barlow H, Shahi SSM. State of the Art: CCS Technologies 2024.; 2024.
3. Panja P, McPherson B, Deo M. Techno-Economic Analysis of Amine-based CO2 Capture Technology: Hunter Plant Case Study. Carbon Capture Sci Technol. 2022;3(December 2021):100041.
4. Al-Juaied M. Amine Scrubbing for CO2 Capture.; 2021.
5. Jiang K, Li K. Harvesting CO2 reaction enthalpy from amine scrubbing. Energy. 2023;284(October):129268.
6. Adams D. Flue Gas Treatment for CO2 Capture. IEA Clean Coal Centre; 2010.
7. Shaw D. Cansolv CO2 capture: The value of integration. Energy Procedia. 2009;1(1):237-246.
8. Paul-Emmanuel Just. Testing of CANSOLV DC-201 CO2 Capture System at the National Carbon Capture Center.; 2017.
9. Linde/BASF. Carbon Capture, Storage and Utilisation.; 2024.
10. Shah M. Engineering Design of a Linde-BASF Advanced PostCombustion CO2 Capture Technology at a Linde Steam Methane Reforming H2 Plant.; 2022.
11. Gorset O, Knudsen JN, Bade OM, Askestad I. Results from Testing of Aker Solutions Advanced Amine Solvents at CO2 Technology Centre Mongstad. Energy Procedia. 2014;63:6267-6280.
12. Dubois L, Costa A, Mouhoubi S, De Weireld G, Thomas D. Postcombustion CO2 capture process by absorption-regeneration applied to cement plant flue gases: techno-economic comparison between the use of a demixing solvent technology and an advanced process configuration. SSRN Electron J. 2022;32(October).
13. Pérez-Calvo JF, Mazzotti M. Techno-economic assessment of postcombustion CO2 capture using aqueous piperazine at different flue gas compositions and flowrates via a general optimization methodology. Int J Greenh Gas Control. 2022;114:103587.
14. McPherson B. CARBONSAFE ROCKY MOUNTAIN PHASE I: ENSURING SAFE SUBSURFACE STORAGE OF CARBON DIOXIDE IN THE INTERMOUNTAIN WEST.; 2018.
15. Fout T, Zoelle A, Keairns D, et al. Cost and Performance Baseline for Fossil Energy Plants Volume 1a: Bituminous Coal (PC) and Natural Gas to Electricity Revision 3. Vol 1a.; 2015.
16. Yun S, Oh SY, Kim JK. Techno-economic assessment of absorption-based CO2 capture process based on novel solvent for coal-fired power plant. Appl Energy. 2020;268(November 2019):114933.
17. IEA. Retrofit of CO2 Capture to Natural Gas Combined Cycle Power Plants.; 2005.
18. Li L, Voice AK, Li H, et al. Amine blends using concentrated piperazine. Energy Procedia. 2013;37:353-369.
19. Loachamin D, Casierra J, Calva V, Palma-Cando A, Ávila EE, Ricaurte M. Amine-Based Solvents and Additives to Improve the CO2 Capture Processes: A Review. ChemEngineering. 2024;8(6):129.