
Photo: BG4US |
21 August 2018 - An unusual sight now greets drivers travelling down the N272 in North Brabant, the Netherlands. One of the first bio-based safety guardrails installed in Europe lines a 20-metre stretch on both sides of the road. The construction replaces metal elements from conventional guardrails, notably substituting their environmentally problematic zinc oxide coating.
“Some 19 tonnes of zinc leach out of guardrails each year in the Netherlands alone,” says Harm Jan Thiewes of the company Millvision, based in the village of Raamsdonk, also in North Brabant. “This metal is toxic for the environment.”
The zinc oxide coating is designed to protect steel rails from rusting, but its own degradation can contaminate groundwater, leach into soils and impact biodiversity. Plants, birds and snails found near motorways tend to suffer from unusually high concentrations of zinc in their metabolism.
Zn-free
As part of the LIFE-funded BG4US project, Millvision is processing plant fibre into green and durable building materials for environmentally sustainable guardrails. Feedstock ingredients include potato waste from chip producers and roadside grass. Mr Thiewes says that this local to local approach lies at the heart of many green solutions proposed by Millvision. It meets the objectives of the EU action plan for the circular economy while profiting both the environment and local communities.
Another potential beneficiary of substituting metal in road infrastructure is the global climate. Manufacturing steel, the main component in guardrails, currently emits vast amounts of carbon dioxide. Preliminary studies suggest that replacing it with bio-based materials would bring down the carbon footprint of guardrail production processes.
The BG4US consortium is still fine-tuning recipes to optimise the properties of its bio-based materials. Its partners are combining bio-composites with steel components and pulling them though a mould to shape guardrail components that can withstand the elements without harming the local environment.
“Biological materials don’t poison the environment and they don’t corrode,” says Mr Thiewes. “But it remains to be seen how well they survive over time.”
Test of time
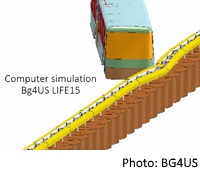
The project plans on installing several hundred metres of guardrails in 2020 to demonstrate the merits of bio-based materials under real-life conditions. Millvision is already investigating a business plan with its partners to roll out the technology on a broader scale. With tightening EU rules on industrial emissions and tens of thousands of kilometres of motorways extending across Europe, green guardrails present a potentially vast market opportunity.
Source : Life Programme | European Union, 1995-2018